The current model is the widespread product recently developed targeting our entry-to-intermediate level customers and migrant construction workers. We developed the current product based on the composition merits we incorporated from similar products of Comall International when we collaborated with them in our early years. Due to its exquisite composition and production, it demonstrates impressive efficacy and becomes one of our company's best-selling product. It is incomparable to those crudely made imitators. The voltage of the current product is 380V, if you are looking for a model with different voltage, please consult us directly.
Â
Product Structure and Characteristics:
- An distinguishing ball bearing wheel composition, ensuring swinging angle to be handily accurate and structure to be firm
- A minimal gap between the operation platform and seating panel, in favor of remnants slightly sliding apart rather than striking them away
- The original swinging head is supported by an exquisite bearing combination, ensuring a satisfying cutting efficacy
- Equipped with a detachable stand whereby the operation platform can be adjusted in height, in favor of both sedentary and mobile use Â
Â
The Four Grand Breakthroughs for the Third Generation Amelioration:
- Merging the saw blade's arresting device and operation handle, simplifying the exterior yet amplifying the beautification
- Due to the blade's stopping device migrated to center, the distance of the bearing shafts of the blade's axis has been amplified; this amelioration is very critical since it increases the stability of the saw, ensures a better cutting result, and guarantee a longer longevity
- The swinging-stabilizing device of the head has been changed from screwing lock to thumb lock, making control more convenient and avoiding it from losing
- Supplemented with an automatic diesel spray device during cutting, ensuring the cooling spray function to be more reasonable and humanized
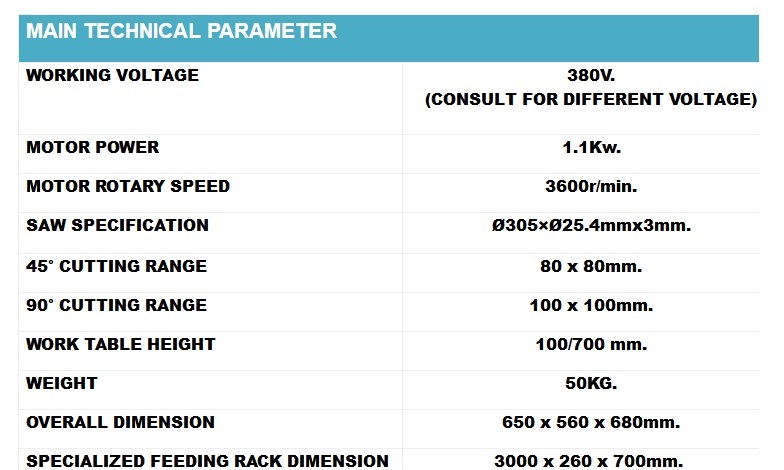
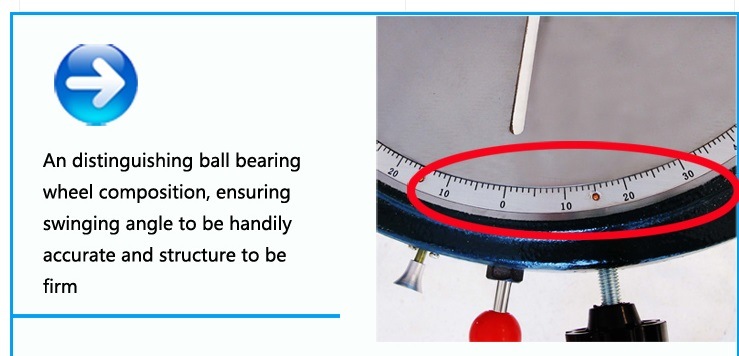
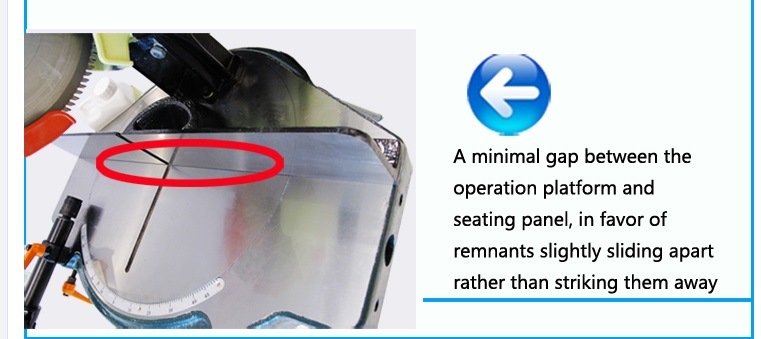
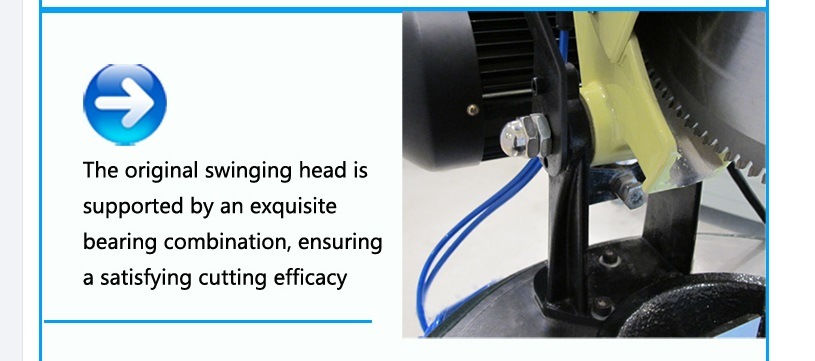
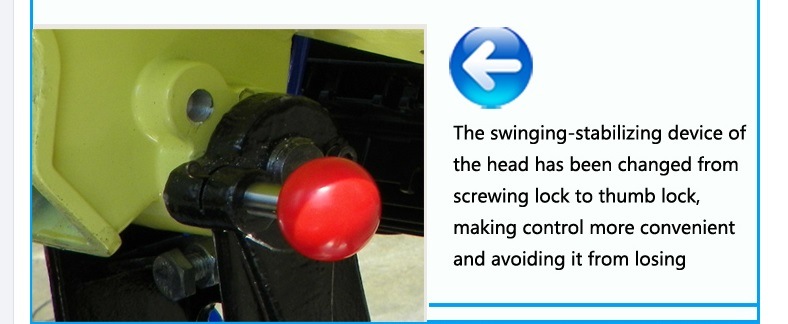
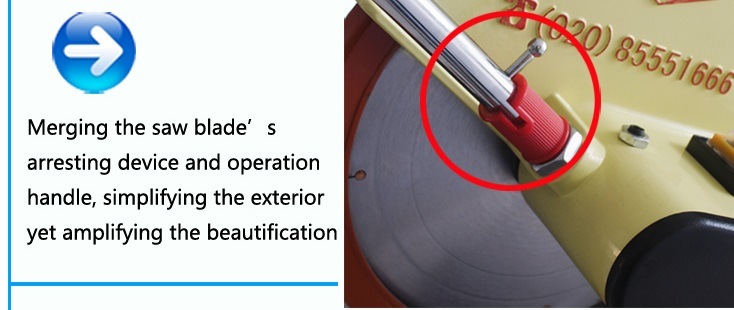
Â
"Gravity Die Casting. A permanent mould casting process, where the molten metal is poured from a vessle of ladle into the mould, and cavity fills with no force other than gravity, in a similar manner to the production of sand castings, although filling cn be controlled by tilting the die."
Gravity Die Casting
Sometimes referred to as Permanent Mould, GDC is a repeatable casting process used for non-ferrous alloy parts, typically aluminium, Zinc and Copper Base alloys.
The process differs from HPDC in that Gravity- rather than high pressure- is used to fill the mould with the liquid alloy.
GDC is suited to medium to high volumes products and typically parts are of a heavier sections than HPDC, but thinner sections than sand casting.
There are three key stages in the process.
- The heated mould [Die or Tool] is coated with a die release agent. The release agent spray also has a secondary function in that it aids cooling of the mould face after the previous part has been removed from the die.
- Molten metal is poured into channels in the tool to allow the material to fill all the extremities of the mould cavity. The metal is either hand poured using steel ladles or dosed using mechanical methods. Typically, there is a mould [down sprue" that allows the alloy to enter the mould cavity from the lower part of the die, reducing the formation of turbulence and subsequent porosity and inclusions in the finished part.
- Once the part has cooled sufficiently, the die is opened, either manually or utilising mechanical methods.
Advantages
- Good dimensional accuracy
- Smoother cast surface finish than sand casting
- Improved mechanical properties compared to sand casting
- Thinner walls can be cast compared to sand casting
- Reverse draft internal pockets and forms can be cast in using preformed sand core inserts
- Steel pins and inserts can be cast in to the part
- Faster production times compared to other processes.
- Once the tolling is proven, the product quality is very repeatable.
- Outsourced Tooling setup costs can be lower than sand casting.
Gravity Casting Parts,Aluminum Alloy Gravity Casting Parts,Aluminum Gravity Die Casting Parts,Gravity Casting Aluminum Parts
HSI INDUSTRIEL LTD , http://www.hsiindustriel.com