Due to the lack of attention to the maintenance of the monitoring system, many monitoring devices are damaged as soon as they are put into use, for the following reasons. First of all, the management department does not pay enough attention to the maintenance of the monitoring system, and considers that it is not necessary to invest more manpower, material resources and financial resources. Therefore, the management of the monitoring system facilities is ignored in the management process, which leads to the late management and maintenance of the system. The second is that there is no complete and planned implementation plan for monitoring equipment maintenance.
The second is the excessive consideration of the cost-effectiveness of the equipment in the procurement of the monitoring equipment, which neglected the monitoring and maintenance of the monitoring system and the equipment in the later period. Too many brands of monitoring equipment, too many product suppliers, and inadequate after-sales protection measures by manufacturers have led to the use of monitoring equipment for a period of time, equipment failures and damage rates continue to rise, and eventually have to upgrade the original equipment in a large area. Repeated investment and serious waste have occurred.
Monitoring equipment maintenance method
In order to do a good job of monitoring equipment maintenance, the repair center is equipped with corresponding human and material resources (tools, communication equipment, etc.), responsible for the daily monitoring, maintenance, service, management of the monitoring system, and undertakes the maintenance service of the equipment to ensure the monitoring Long-term, reliable, and efficient operation of the system
I. Basic conditions for maintenance
As the old saying goes, "A smart woman is hard to cook without rice", the same is true for the maintenance of the monitoring system. The basic maintenance conditions required for normal equipment maintenance of the monitoring system are "four equals", that is, spare parts are available. , Accessories, tools, instruments.
1, spare parts are available
Generally speaking, the maintenance of each system must establish a corresponding spare parts library, which mainly stores some of the more important equipment that is not easy to repair after damage, such as cameras, lenses, monitors, etc. Once these equipments fail, the system may not run normally and must be replaced in time. Therefore, a certain number of spare parts must be available, and the inventory of the spare parts library must be continuously updated according to whether the equipment can be maintained and the characteristics of the equipment's operating cycle.
2.Accessories
Accessories are mainly additional configurations of various components and modules in the equipment, which can be prepared more, mainly for equipment maintenance. Commonly used accessories include various integrated circuit chips and various circuit discrete components required by the circuit. Other larger equipment must be equipped with certain functional modules for emergency use. In this way, after maintenance, good benefits can be produced with a small investment, saving a lot of money for equipment upgrades.
3, tools and testing equipment
In order to repair the equipment, it is necessary to configure commonly used maintenance tools and inspection instruments, such as various pliers, screwdrivers, electric pens, electric irons, adhesive tapes, multimeters, oscilloscopes, etc., you should also add them at any time if necessary, and you should also yourself Make a test tool such as load simulation.
Second, some precautions in equipment maintenance
During the maintenance of the monitoring system equipment, some situations should be prevented to ensure that the equipment runs as normal as possible. The main work is to prevent moisture, dust, corrosion, lightning, and interference.
1, moisture-proof, dust-proof, anti-corrosion
For various acquisition equipment of the monitoring system, since the equipment is directly placed in a dusty environment, it will have a direct impact on the operation of the equipment, and it is necessary to focus on the maintenance work against moisture, dust and corrosion. If the camera is suspended from the shed for a long time, the protective cover and dust-proof glass will soon be covered with a layer of dust, carbon ash, etc., which is dirty and black, and also corrosive, which seriously affects the viewing effect and also brings equipment. It is damaged, so the dustproof and anticorrosive maintenance work of the camera must be done well. In some places with heavy moisture, the installation position and equipment protection must be adjusted during the maintenance process to improve the equipment's moisture resistance. At the same time, dehumidification measures must be taken frequently to solve the problem of moisture resistance in high-humidity zones.
2.Lightning and interference prevention
As long as anyone who has been engaged in the maintenance of electromechanical systems knows that lightning strikes are common after thunderstorms, which will cause great safety risks to the normal operation of monitoring equipment. Therefore, monitoring equipment must be protected against lightning during the maintenance process. highly valued. The lightning protection measures are mainly to implement a lightning protection grounding network for equipment grounding. An integrated grounding network with a ground resistance of less than 1 ohm should be prepared according to the equipotential scheme to prevent lightning protection grounding of weak electrical systems and power lightning protection grounding networks. Mixed practices to prevent power ground grid clutter from interfering with equipment. The anti-interference principle is to adhere to the principle of separation of strong and weak electricity when wiring, separate power cables from communication cables and video cables, and strictly follow the wiring specifications of the communications and power industries.
The details are as follows:
1. Dust removal and cleaning of the equipment once a quarter, clean up the dust exposed from the monitoring equipment, remove the dust from the camera, protective cover and other parts, and then wipe each lens with anhydrous alcohol cotton to adjust the sharpness to prevent damage. Factors such as machine operation and static electricity suck dust into the body of the monitoring equipment to ensure the normal operation of the machine. At the same time, check and monitor the ventilation, heat dissipation, dust cleaning, and power supply facilities in the equipment room. The outdoor temperature should be -20 ℃ ~ + 60 ℃, the relative humidity should be 10% ~ 100%; the indoor temperature should be controlled at + 5 ℃ ~ + 35 ℃, and the relative humidity should be controlled between 10% ~ 80%. It is left to the computer room for monitoring. The equipment has a good operating environment.
2. According to the operating instructions of each part of the monitoring system, monthly check its technical parameters and the quality of the transmission line of the monitoring system, handle the hidden troubles, assist the supervisor in setting various data such as the usage level, and ensure that each part of the equipment is different. The item functions well and can run normally.
3. Perform a comprehensive inspection of the monitoring equipment parts that are easy to deteriorate once a month. Once the aging phenomenon is found, it should be replaced and repaired in time, such as video head.
4. Clean the dusty part regularly every quarter. If the monitor is exposed to the air, due to the electrostatic effect of the screen, a lot of dust will be adsorbed on the monitor surface, affecting the clarity of the screen. Proof the color and brightness of the monitor.
5. The long-term monitoring equipment is regularly maintained once a month. For example, if the hard disk video recorder works for a long time, it will generate more heat. Once its electric fan fails, it will affect the heat dissipation and prevent the hard disk video recorder from working abnormally.
6. Monitor the operation of the monitoring system and equipment, analyze the operation, and find and troubleshoot in a timely manner. Such as: network equipment, server systems, monitoring terminals and various terminal peripherals. Desktop system operation check, network and desktop system virus defense.
7. Regularly optimize the monitoring system and equipment every month: Reasonably arrange the monitoring network requirements of the monitoring center, such as bandwidth, IP address and other restrictions. Provides monthly monitoring of network performance of the monitoring system, including network connectivity, stability, and bandwidth utilization; real-time detection of all external network attacks that may affect the monitoring of network equipment, real-time monitoring of server operating status, traffic, and intrusion monitoring Wait. Check the abnormal situation and deal with it. Plan and optimize the monitoring network according to user needs; assist in handling server software and hardware failures, and disassembly and assembly of related hardware and software.
8. Provide regular information service once a month: on the first working day of each month, submit the repair, repair, maintenance, and maintenance record form of the previous month to the other party in the form of electronic files.
Handover of engineering and technical data
In order to ensure that the after-sales service department can have better conditions for system maintenance and repair work, the engineering technology department must do the following:
1. When the project is accepted or delivered, the after-sales service personnel must be notified to be present, so that the after-sales service personnel are familiar with the composition of the project as soon as possible, the use situation and the relevant users of the construction unit.
2. After the project is delivered for use, the engineering department and technical department must submit the following materials of the project to the after-sales service department:
(1) All design plans and drawings
(2) Manuals, certificates, test reports, etc. of relevant equipment and equipment. (3) Routine routine maintenance of all completed data systems for the project.
3. The daily routine work of system maintenance is carried out by the after-sales service department. The specific regulations are as follows:
(1) Establish system maintenance work files, and record the daily maintenance work of each engineering system in detail, so that any system can be handed over to any technical staff in this department at any time, without lack of relevant information or management And cannot work.
(2) Since the system is delivered and used, a routine inspection of the system's condition is conducted every two months, and users of the user are invited to accompany the inspection as much as possible. At the same time, actual further training of the use and daily maintenance capabilities of the user can be conducted. And raise.
(3) Starting from the delivery of the system, every six months, the system's key equipment such as camera guns, gimbals, digital video hosts, color displays, monitors, etc. of the CCTV surveillance system, and host systems, detectors, and other equipment of the anti-system, Comprehensively check its performance once to ensure that the system is in good working condition.
(4) From the time the system is delivered to use, a comprehensive inspection of all the equipment and lines of the system is conducted once a year to try to keep the performance of the system in a good state when delivered. If the performance is too long and the performance deviation is too large to affect the overall effect of the system, you should try to convince the user to replace it to ensure the normal use of the system. The specific operation of maintenance work.
Main problems of maintenance
I. Line maintenance
1. The ultra-five network cable has poor tensile resistance. Check whether the cable is broken? Can observe the power supply status of the transformer power indicator? Check whether the transformer works normally?
2. The network cable is disconnected correctly but the power cannot be supplied. Check whether the network socket is damaged? Check whether the transformer works normally?
3. The line power supply is normal and there is no video signal. Check whether the line is broken? The network cable is disconnected correctly. Check whether the twisted pair video transmitter is damaged or the connector is loose. It can be exchanged and detected with other channels. (If the twisted pair video transmitter is damaged, please apply for replacement)
4. I can't control the PTZ with video. Check whether the cable is cut off? The network cable is disconnected correctly. Check whether the dome number corresponds to its channel address code?
Camera maintenance and repair
1. The outer transparent cover is a highly transparent acrylic sheet, which is pressed into a hemispherical shape at one time. The camera needs good light transmission. Do not wear the transparent cover to blur the camera image. Keep the transparent cover clean and bright. When you find that the image is blurred, check that the outside of the transparent cover is not dirty or scratched. If there is dust inside, please remove the whole machine carefully, open the transparent cover of the camera under safe conditions, and clean the dust carefully.
2. There are not only electronic circuits but also mechanical devices inside. Its small size and limited internal space make the mechanical devices relatively small. Remember to handle them lightly, and do not drop or touch them.
Third, power failure
The source may be incorrect as follows: the power supply line or power supply voltage is incorrect, the power is insufficient (or the diameter of a power supply line is not enough, the voltage is too large, etc.), the transmission line of the power supply system is short-circuited, disconnected, or transient Wait. In particular, equipment damage may occur due to incorrect power supply or transient overvoltage. Therefore, in the system debugging, before the power supply, we must carefully check and check, and should not be taken lightly.
Fourth, line failure
If it is not handled properly, especially the line connected to the equipment is not handled well, open circuit, short circuit, poor insulation between wires, incorrect wiring, etc. will cause problems such as equipment damage and performance degradation. In this case, you should calmly analyze according to the failure phenomenon, and judge which faults occur on several lines due to which lines have connection problems. This will narrow the scope of the problem. It is particularly worth pointing out that it is common for a camera with a gimbal to move and take a long time to cause the connection to come off or break. Therefore, special attention should be paid to the connection between the equipment and various lines in this case to meet the requirements of long-term operation.
Monitor and maintain files and services
1. The administrative department should organize and archive the relevant information of all users, and receive and organize the user's fault records.
2. Every day after going to work, the fault records to be handled will be handed over to the after-sales service manager. The after-sales service manager can arrange work according to the specific situation.
3. The administrative department and the after-sales department cooperate to establish a maintenance work record card. Each time the customer reports an obstacle, from receiving the message to sending related technical personnel to handle it, as well as the processing process and processing results, the user opinion should have a complete record, and It will be included in the evaluation system as the work evaluation standard of relevant personnel.
4. General troubleshooting, after-sales service personnel should complete the report the next day after the report, the failure of major equipment, affecting the use of the system, within 4 hours after the report is completed, the specific operation of maintenance work, particularly serious failures Those who cause system paralysis shall be present within 2 hours after receiving the report.
5. Carry out the warranty work according to the relevant national regulations. If it belongs to the scope of the warranty, the user must be guaranteed. For the equipment that will affect the overall work of the system, a backup machine should be provided during the warranty period, or according to the site conditions, take feasible measures The user can continue to use the basic functions of the system normally, and minimize the inconvenience caused to the user by the warranty work.
High Speed CNC Drilling & Marking Line For Angles
Efficiency Case:
l 250*250*32mm
angle size, hole dia. 22mm, SANDVIK drill bits, rotation speed 2200rpm, one
hole takes 6 seconds.
l One day (8 hours) gets 65 tons output.
l 9 minutes finish
one angle length of 14 meters, with 60 holes.
The production line is composed of infeed transfer table unit, rotating
loading unit, feeding conveyor unit, marking unit, two drilling units, outfeed
conveyor unit, hydraulic system and electrical control system etc.
â–²Adopt CNC technology, servo motor infeeding,
with high efficiency, stable working precision.
â–²Key hydraulic, pneumatic and electric elements are all domestic
and international brand.
â–²Easy programming and can directly use the program
data made by lofting software.
â–²Software with Chinese, English interface, easy
operation, and can display the drawing of workpiece.
â–²Loading, marking, drilling and unloading are all performed
automatically.
â–²Just need to input size of work piece,
diameter of holes, stadia and quantity of workpiece when edit program, or
use CAD/CAM lofting software direct conversion.
â–²The machining line is installed with supporting
&straight pressing device.
â–²With avoided shearing functions, so as to process fixed length
angles.
â–²With self-diagnosis failures function.
â–²Shearing unit is optional, using double blades cutting.
Drilling Unit (High Speed Drill Bits)
Samples:
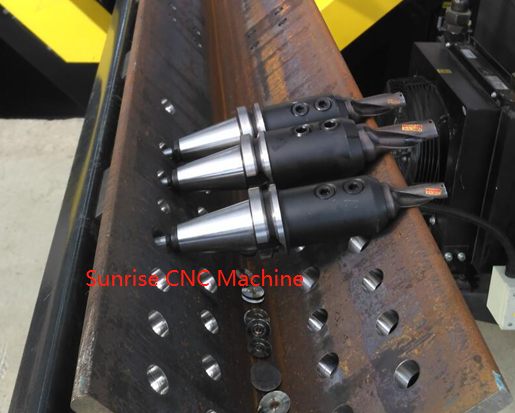
6 spindles separately controlled by 6 servo motors
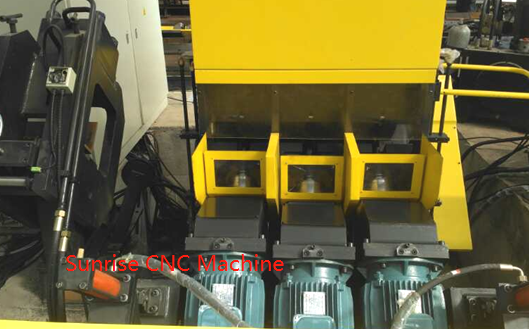
Close type marking
unit, more stable and longer life
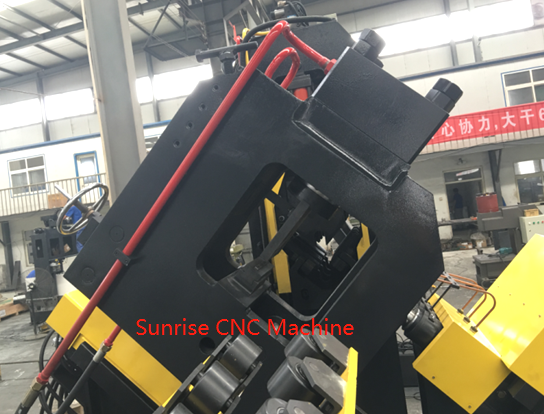
Marking Unit:
This unit is consists of fixed lathe bed, movable
lathe bed, hydraulic pressure head and manual adjustment device. According to
the order of computer, the unit marks on places required on the drawings. For
making the marks clear and endurable, and avoiding the angle steel abrades
character heads, it adds the functions of loading oil cylinder and lifting
movable lathe bed. For satisfying the processing scope, it adds manual
adjustment device, which can change the position of characters to adapt
different standards angle steel.
Workpiece
Table: It is driven by engine and retarder
through chain wheel and chain. There are three long axis and six self-control
shaft couplings to achieve synchronization of the chains. Thus the angle steel
will be stable and make lower noise during feeding process. The function of
this part is that feed angle steel into the chute and prepare to be taken by
the clamp device.
Overturning Rack: It is driven by engine and retarder through chain wheel and chain.
Thus it achieves synchronization of swivel arm of the four clamps devices
through long axis and shaft couplings. The function of this part is to take
angle from conveyor trough to feeding conveyor.
Angle Drilling Machine
Angle Drilling Machine,Steel Construction Drilling Machine,Angle Rocker Drilling Machine,CNC Angle Drilling Machine
Shandong Sunrise CNC Machine Co., Ltd , https://www.scmcnc.com