Description of Jaw crusher:
Jaw crushers can be used together with mine-selecting equipments and gravel processing equipments as well as used independently. The Jaw crusher is used for Primary crushers and Secondary crushers for crushing all kinds of minerals and rocks with compressive strength less than 320 MPa. There are two types of Jaw crusher: Coarse jaw crusher and Fine jaw crusher. We Henan ZhengKuang Machinery also manufacture Mobile jaw crusher, Single toggle jaw crusher and otherJaw breakers.
Working principle of Jaw crusher:
The strip and strip pulley are driven by a motor, and the moving jaw moves up and down via eccentric shaft. The angle between fixed jaw and moving jaw becomes smaller when the moving jaw runs down, then the materials are crushed into pieces. It will become bigger when the moving jaw runs up. The moving jaw board leaves the fixed jaw board under the action of pole and spring, and then the end products come out from the crushing cavity. And also, Jaw crusher is always used as the Primary jaw crusher.
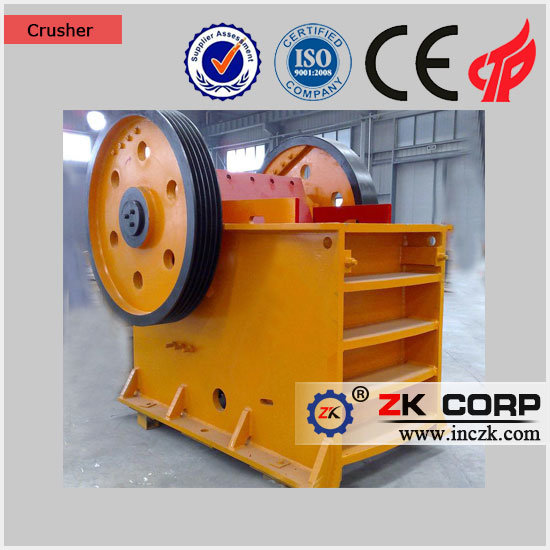
Jaw crushers Performance and features:
1. Crushing cavity is deep and there is no dead area, which improves feeding capacity and output;
2. High reduction ratio and uniform final product size;
3. Spacing piece type discharge-hole adjustment device is reliable and convenient;
4. Reliable and safe lubrication system, convenient replacement of parts and small work load of maintenance;
5. Simple structure, operational reliability and low operation cost;
6. Energy-saving: Single machine can save energy by 15% to 30%; The system can save energy by over 30% to 60%;
7. Large adjustment range of discharge hole can meet the demands of different users;
8. Low noise and little dust;
9. Simple structure, convenient maintenance and use; Stable performance, low operation cost; High reduction ratio.
10. The outlet employs pad-style adjustment devices, convenient and reliable, and increase the flexibility of the equipment.
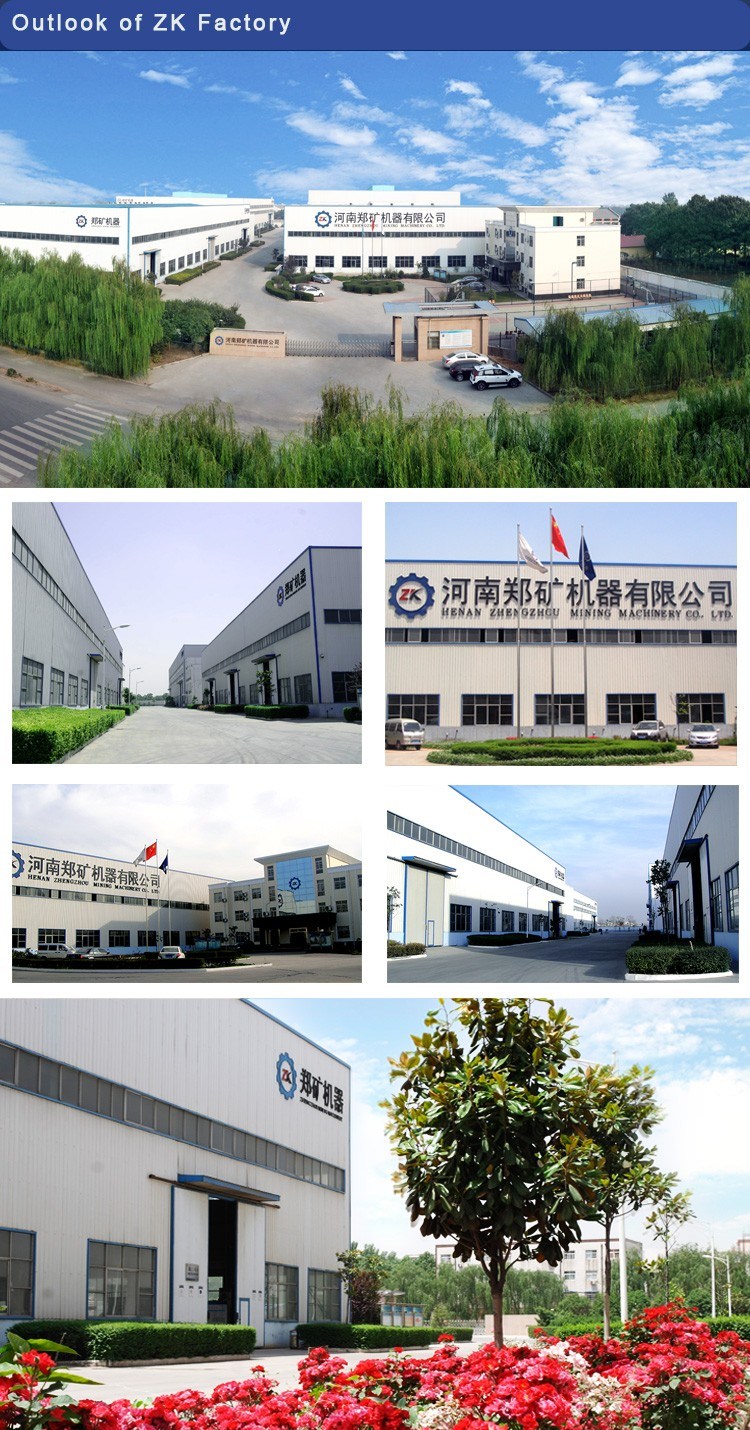
Company Name: Henan Zhengzhou Mining Machinery Co., Ltd.
Official Website: http://www.inczk.com/ & http://www.zkcomp.com/
24-hour Free Sales Consulting Phone: 861-0371 -5590 2866.
Company Address: Qiaolou caizhai industrial estate, Xingyang city, Henan Province
Please pay attention to the company's other products:
Price of rotary kiln: http://www.zkcomp.com/calcining/558. Html
Rotary Kiln: http://www.inczk.com/Products/459. Html
Preheater: http://www.zkcomp.com/calcining/605. Html
Cement Mill: http://www.inczk.com/Products/460. Html
Rotary Dryer: http://www.zkcomp.com/calcining/564. Html
Raw Mill: http://www.inczk.com/Products/1373. Html
Ball Mill: http://www.zkcomp.com/grinding/582. Html
Model | Feed Opening (mm) | Max. feeding size (mm) | Adjusting range of discharge opening (mm) | Capacity (t/h) | Rotation speed of eccentric shaft (r/min) | Motor power (kw) | Total weight (t) | Dimensions (L*W*H)(mm) |
PE-150*250 | 150*250 | 125 | 10-40 | 1-3 | 250 | 5.5 | 0.8 | 720*660*850 |
PE-200*300 | 200*300 | 180 | 15-50 | 2-6 | 260 | 7.5 | 1.2 | 910*750*990 |
PE-200*350 | 200*350 | 180 | 18-70 | 3-10 | 260 | 11 | 1.5 | 1000*870*990 |
PE-250*400 | 250*400 | 210 | 20-60 | 5-20 | 300 | 15 | 2.8 | 1300*1090*1270 |
PE-400*600 | 400*600 | 340 | 40-100 | 16-60 | 275 | 30 | 7 | 1730*1730*1630 |
PE-500*750 | 500*750 | 425 | 50-100 | 40-110 | 275 | 55 | 12 | 1980*2080*1870 |
PE-600*750 | 600*750 | 500 | 150-200 | 80-240 | 275 | 55 | 15.8 | 2070*2000*1920 |
PE-600*900II | 600*900 | 500 | 65-160 | 50-180 | 250 | 55 | 17 | 2190*2206*2300 |
PE-750*1060 | 750*1060 | 630 | 80-140 | 110-320 | 250 | 110 | 29 | 2660*2430*2800 |
PE-800*1060 | 800*1060 | 640 | 130-190 | 130-330 | 250 | 110 | 29.8 | 2710*2430*2800 |
PE-830*1060 | 830*1060 | 650 | 160-220 | 150-336 | 250 | 110 | 30.7 | 2740*2430*2800 |
PE-870*1060 | 870*1060 | 660 | 200-260 | 190-336 | 250 | 110 | 31.5 | 2810*2430*2800 |
PE-900*1060 | 900*1060 | 685 | 230-290 | 230-390 | 250 | 110 | 33 | 2870*2420*2940 |
PE-900*1200 | 900*1200 | 750 | 95-165 | 220-450 | 200 | 110 | 52 | 3380*2870*3330 |
PE-1000*1200 | 1000*1200 | 850 | 195-265 | 315-500 | 200 | 110 | 55 | 3480*2876*3330 |
PE-1200*1500 | 1200*1500 | 1020 | 150-350 | 400-800 | 180 | 160 | 100.9 | 4200*3300*3500 |
PE-1500*1800 | 1500*1800 | 1200 | 220-350 | 500-1000 | 180 | 280 | 122 | 5160*3660*4248 |
PE-1800*2100 | 1800*2100 | 1500 | 300-400 | 600-1200 | 160 | 400 | 150.6 | 6210*4013*4716 |
PEX-150*750 | 150*750 | 120 | 18-48 | 8-25 | 320 | 15 | 3.8 | 1200*1530*1060 |
PEX-250*750 | 250*750 | 210 | 25-60 | 13-35 | 330 | 30 | 5.5 | 1380*1750*1540 |
PEX-250*1000 | 250*1000 | 210 | 25-60 | 16-52 | 330 | 30 | 7 | 1560*1950*1390 |
PEX-250*1200 | 250*1200 | 210 | 25-60 | 20-61 | 330 | 37 | 9.7 | 2140*1660*1500 |
PEX-300*1300 | 300*1300 | 250 | 20-90 | 16-105 | 300 | 55 | 15.6 | 2720*1950*1600 |
Sand Casting is used to produce a wide variety of metal components with complex geometries. These parts can vary greatly in size and weight, ranging from a couple ounces to several tons. Some smaller sand cast parts include components as gears, pulleys, crankshafts, connecting rods, and propellers. Larger applications include housings for large equipment and heavy machine bases. Sand casting is also common in producing automobile components, such as engine blocks, engine manifolds, cylinder heads, and transmission cases.
Sand casting, the most widely used casting process, utilizes expendable sand molds to form complex metal parts that can be made of nearly any alloy. Because the sand mold must be destroyed in order to remove the part, called the casting, sand casting typically has a low production rate. The sand casting process involves the use of a furnace, metal, pattern, and sand mold. The metal is melted in the furnace and then ladled and poured into the cavity of the sand mold, which is formed by the pattern. The sand mold separates along a parting line and the solidified casting can be removed. The steps in this process are described in greater detail in the next section. In sand casting, the primary piece of equipment is the mold, which contains several components. The mold is divided into two halves - the cope (upper half) and the drag (bottom half), which meet along a parting line. Both mold halves are contained inside a box, called a flask, which itself is divided along this parting line. The mold cavity is formed by packing sand around the pattern in each half of the flask. The sand can be packed by hand, but machines that use pressure or impact ensure even packing of the sand and require far less time, thus increasing the production rate. After the sand has been packed and the pattern is removed, a cavity will remain that forms the external shape of the casting. Some internal surfaces of the casting may be formed by cores.
Sand casting is able to use of almost any alloy. An advantage of sand casting is the ability to cast materials with high melting temperatures, including steel, nickel, and titanium. The four most common materials that are used in sand casting are shown below, along with their melting temperatures
Materials Melting temperature
Aluminum alloys 1220 °F (660 °C)
Brass alloys 1980 °F (1082 °C)
Cast iron 1990-2300 °F (1088-1260 °C)
Cast steel 2500 °F (1371 °C)
The material cost for sand casting includes the cost of the metal, melting the metal, the mold sand, and the core sand. The cost of the metal is determined by the weight of the part, calculated from part volume and material density, as well the unit price of the material. The melting cost will also be greater for a larger part weight and is influenced by the material, as some materials are more costly to melt. However, the melting cost in typically insignificant compared to the metal cost. The amount of mold sand that is used, and hence the cost, is also proportional to the weight of the part. Lastly, the cost of the core sand is determined by the quantity and size of the cores used to cast the part.
Sand casting process advantages
Can produce very large parts
Can form complex shapes
Many material options
Low tooling and equipment cost
Scrap can be recycled
Short lead time possible
Applications:
Construction Machine Parts,Scaffolding Parts,Engine blocks and manifolds, machine bases, gears, pulleys, agriculture parts,Marine Parts,medical parts,hardware, automobile parts,ect.
Sand Casting
Sand Casting,Aluminum Sand Casting,Stainless Steel Sand Casting,Sand Precision Casting
Ningbo City Yinzhou Ruican Machinery Co.,Ltd , https://www.kstcasting.com